How to define precision injection molding machine chapter 2
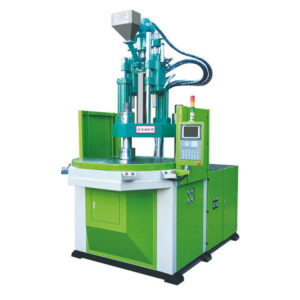
Rotary table vertical injection machine
How to define precision injection molding machine chapter 2
The accuracy of the displacement sensor is required to reach at least 0.1 mm,so the metering stroke,injection stroke and thickness of the residual mat (injection monitoring point) can be strictly controlled,also ensure every shot accurately and improve the molding accuracy of the product.
2.barrel and nozzle temperature should be controled accurately
When the temperature control system is heating, the overshoot should be small and the fluctuation of temperature need to be small. Precision injection molding adopts PID proportional, integral and differential temperature control to achieve temperature accuracy near ±1 °C. The temperature control accuracy of ultra-precision injection molding machine is around ±0.1 °C, and the temperature deviation can be stably controlled between ±0.2 °C.
3.hydraulic oil temperature of injection molding machine needs to be controlled
The change of oil temperature leads to injection pressure fluctuate. It is necessary to cooled by a cooling device to stabilize between 50°C and 55°C.
4.Requirements of mold temperature
The temperature of mould not only seriously influence on the part of later heat shrinkage and the apparent quality and crystallinity but also affect mechanical property. If cooling time is the same, the thickness of the products which have low mold cavity temperature is greater than the thickness of the products which have higher temperature.
Hydraulic system of precision injection molding machine
1.oil system needs to be utilized proportional pressure valve such as proportional flow valve or closed loop variable pump system.
Whether quantitative pump hydraulic system or variable pump hydraulic system, both have proportional valve to limite output pressure and flow rate of oil pump for achieving proportional linear adjustment.
In direct pressure clamping mechanism, the mold oil line and the injection oil line should be separated.
This requirement is for direct pressure injection molding machine, because when the direct pressure injection molding machine clamp mould, it starts to inject the melt and the fill into mold cavities immediately.At the same time,the oil must be filled with the clamping cylinder to form high clamping pressure.
Otherwise, the middle plate will be backed by filling pressure and the mold expansion force, which is not allowed. So,the clamping oil line and the injection oil line have to be separated. Furthermore, it also will occurs problem with oil pump overload by oil filled with clamping cylinder and injection cylinder simultaneously.As a result,it affects injection speed and system stability.
Written by Jerry-Ho
Leave a Reply
Want to join the discussion?Feel free to contribute!